wiseguy
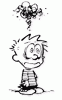 Guru
 Joined: 21/06/2018 Location: AustraliaPosts: 1206 |
Posted: 01:11pm 28 Mar 2023 |
|
|
|
Starting to get a second wind with my inverter progress (or lack of it...). I recently bought two 3kW Aerosharps for $25 each as I am still trying to avoid a full toroidal rewind. My plan was to consider using two transformers that could be driven in parallel for plenty of grunt. Ideally though at night for conservation it would be good to only have the one transformer with its associated magnetising current instead of two.
I have decided to abandon the two smaller transformers that I have been using to date as despite them working ok they are still a bit undersized for the eventual loads I want to be able to drive. I am confident that the grunt issue will be resolved when I get the right recipe for my HF choke which appeared to have a bit too much inductance.
I also want to be able to work on the inverter and simply swap chokes etc without it all being jammed into too small an enclosure and thus any changes became a major exercise. So a new chassis and layout is also in the works. Eventually I will have a wheeled trolley with nano inverter, battery storage, battery charger, grid feed inverter and a few other bits all in one easily moved and easily worked on trolley. The Aerosharp transformers looked identical except one winding was black and white wires, the other was black and off white - a slight tan colour. The label describes the transformer as 230VAC for the black and white and 250V for the Blue & Red winding.
One could be forgiven to expect that the black and white winding was for the mains input but this is not so, they are from the inverter drive, the Red and Blue 250V winding is for the mains L & N connection.
Initially I had hoped the mains winding would be the inner winding and I could simply remove the outer winding and slap a new primary on it and job done. However as the voltages on the existing two windings are fairly close perhaps they could be put in parallel for an ultra low loss mains winding? I worked out the volts per turn by throwing 10 turns through the core and driving the primary with 100V and was able to determine that the primary had 212T and the secondary had 195 turns. All I had to do was add 17T to the 195T and they would both be 212T. So far so good.
Whilst the transformer was already on the bench, I placed the second unit next to it and wired the primaries in parallel, joined the secondary blacks and whites together and slowly wound up the Variac.
I noted the power consumption was slightly more than the addition of the 2 idling currents, so I placed an amp clamp on one of the secondary wires and noted that there was ~ 1.1A flowing ! So I disconnected the bridged secondary and there was ~ a 0.9V difference. I had already established on the first transformer that 1 turn was ~ 1.13V - what gives, something doesn't add up !! So transformer 2 behaves slightly different, I re did the turns evaluation and the second transformer has 215T on the primary and 197T on the secondary.
The only possible way to drive them in parallel is to add 3 turns to the first transformer primary (212), 20 turns to its secondary(195) then they are both at 215T and then add 18 turns to the second transformers secondary (197) and voila now we have 4 x 215T windings. Now simply add a 27T primary to both units and job done.
I am less than ecstatic at this whole proposition, so I am considering buying yet a third 3kW Aerosharp to find out what arbitrary primary and secondary windings it has. Would it be the same as one of the two I have or will there be a third variant ?
Just as a note of interest, the first transformer with the 212T primary at 240V it draws ~ 12.5W and at 220V it is ~ 9.7W. The second transformer with the 215T primary draws 9.72W at 240V and at 210V (not a typo) it is ~ 7W. These are quite different values, the second transformer idling power at 240V is only ~77% of the first unit.
This leads me to my next thoughts that maybe if inverter power generation requirement (overnight) for longish periods is less than 50W (an arbitrary guess figure) the voltage could be reduced to 210 or 220VAC to reduce wasted magnetising power and as soon as power is greater than 50W it could revert to 230/240, whatever is normal for a given set up. When there are a few overcast days and perhaps not a huge storage bank, every bit saved helps.
I of course am considering employing a complicated (over complicated?) setup where if the power requirements of the load exceed 3 or 4kW then the second transformer is switched in parallel to assist with energy throughput and minimise losses and heat build up. At this stage I dont think a separate power H bridge driver from a common controller is required as I think the one H bridge with the 16 x HY5608s should cope ok.
Last comment obviously I would use the transformer with the lowest magnetising current for the overnight economy and switching the other lossier unit when I need some bulk power.
I would be pleased to receive comments, suggestions, criticisms or advice about what to do with transformer quandry I seem to be facing. Edited 2023-03-28 23:18 by wiseguy |