wiseguy
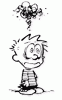 Guru
 Joined: 21/06/2018 Location: AustraliaPosts: 1206 |
Posted: 05:42am 20 Apr 2024 |
|
|
|
The Inverter code is nearing completion, the most recent version I received last night, I cannot fault its operation, but still testing.
The setup/calibration is realtively simple, the default values essentially would allow the inverter to run for a 48V system, when the code is loaded. However, for accuracy there are calibrations for Vcap & Vin, both calibrated in one step, then there is the calibration for AC output Voltage and current. Please be aware that the AC readouts whilst quite accurate for resistive loads should not be totally relied on for exact accuracy as they are essentially peak readings but calibrated as for RMS.
I recommend using a true RMS meter when calibrating the AC volts and amps. For stress free settings of AC Amps and over current trip at for instance 5kW loads, a 10T winding through the current sense transformer allows 1 A to look like 10A.
My method is to place a short length of 2.5mm enamelled wire through the current sense transformer, as the main current conductor from the inverter to the load. Now from the load side connect a 1mm enamelled wire and wind through the current sense transformer 9 more times and terminate the 3 wires onto a terminal block or similar.
Now a 500W load using the extra 9T will calibrate as for a 5kW load whilst only supplying a load of 2A instead of 20A. Another method is to use a 240V to 6 or 12V transformer wired with a 0.5 - 1 ohm resistor in series to a 1mm enamelled 10T winding and using a Variac (yes its coming....) and AC amp-clamp meter, you can calibrate the inverter AC Amp meter and the over current trip point as required.
The display shows the applied input voltage (Vin), the actual Voltage of the main capacitor bank (Vcap) The 240V Mains output Voltage and Current, the % of PWM power drive 0.0 - 99.9% and heatsink and toroid temperatures and status of the 2 Fans. There is a "mains up", 12V open drain FET output to switch a relay that automatically connects the mains to the load when the ramp up is complete.
The test mode of the control PCB will allow the inveters PWM/Opto drive to run despite low capacitor bank and input voltages. This function is invaluable for initial testing or repair. Simply put the J11 link to test and apply 16V to the controller, the LCD reports "Test mode" the main capacitor bank can now be powered from a variable DC supply. A sinewave is generated on the toroids output from as low as 1VDC (about 7VAC from the mains). The drive waveforms & current consumption etc can be monitored as you advance the FET Power section voltage up to its normal voltage.
I had to temporarily stop work on the new Variac PCB testing, to concentrate on the software creation and testing of the main inverter which I (and probably Poida) underestimated the total amount of work required to beat it into shape.
Hopefully in the near future (a week if all goes well) I can tell you they are both finished and ready for manufacture, after we work out who wants what and how many.
I will post a picture soon of the actual display with the inverter working. Edited 2024-04-20 17:49 by wiseguy |