It really does help if you have the right test equipment.
The power supply arrived last Thursday as did the smaller gate resistors. I fitted the fets to the second power board with the smaller resistors.
Following Wiseguy's test procedure everything checked out ok on the bench with both boards, hooked up to the toroid and all was good (both power boards and both nano boards were tested and all worked).
I guess it must have been an unstable supply coming from the batteries and light globe or fuse when loaded with the toroid after all. I'm happy to be the village idiot if it saves someone else from making the same mistake!
Eventually wound it up to 54V in, 235V out, this is with the nano board and fet board powered by the variable supply:
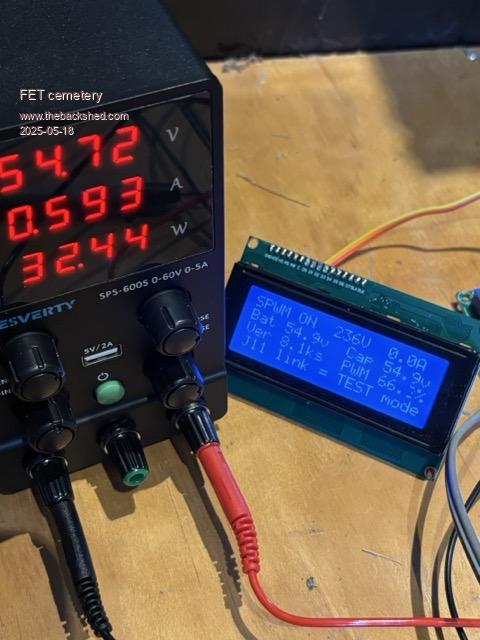
The transformer makes a nasty hum if the voltage is wound up too fast but settles down pretty quickly.
Waveform is ok.
Couldn't help myself, I hooked it up to the house battery with a 32A breaker on the DC side and ran a 1kW heater for 20 minutes or so, bit of a hum from the transformer and the waveform wasn't as pretty but this was using the power board with the big resistors and some fairly untidy wiring that could easily have been picking up switching noise.
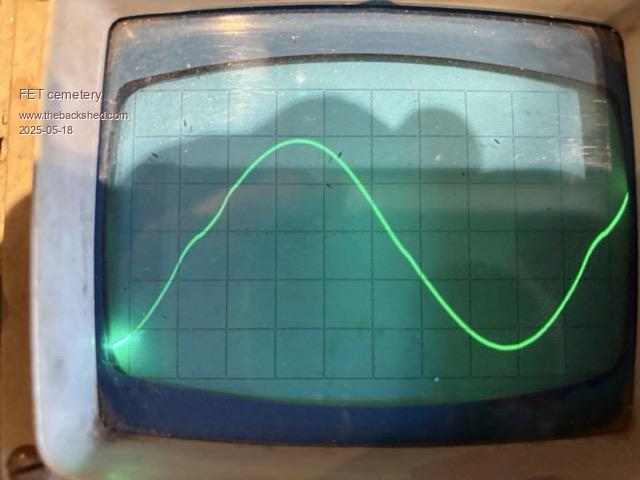
The bias supplies and regulators were slightly above ambient, 5 degrees or so, nothing else was even remotely warm. No air movement, power board lying flat with the heatsink underneath it.
Efficiency was a whisker under 95%, take away the 30W standby power and the conversion efficiency is nudging 98% at 1kW. Impressive!
Time to build a cabinet for it and wire it up properly.
Thank you to everyone who has helped me get this far!