UPDATE .....
I started this project in late 2021, i have other projects so this has been delayed, but finally i am getting their, oh yea.
The Case of the NEW MODERN PLANTE lead acid battery.
Over Christmas the case has been undergoing fluid testing. All good.
Remember folks, this is a project and concept that will be official published, tech drawings, designs and jigs design, and loads of colour photos, for anybody on this Planet to make their own.
Designed and Now making the steel moulds so the internal plate joining lead bus bars can be easily constructed/cast.
Questions from David, and my Answers.....
Q.
Will the plate assembly be easy to lift out to clean sheddeed material from the botton or will the thickness and construction of the plates avoid anything falling to the bottom?
Yes, the assembled plates will be easy to lift out, as the the top of the battery will be removable. The negative and positive terminal post will be 10mm stainless steel, so undo the 2 stainless steel nuts and shims and the case top just lifts off after the 12off top 4mm stainless bolts are removed. The top is sealed with a tested silicone that can be cut with knife.
The plates sit on the case bottom strips that are 25mm to the sump. They also sit on the intetnal lip and the lead bus bars. These plates are solid so the lead dioxide active surface is formed as the battery is worked. They are NOT a grid matrix with a impregnated lead dioxide.
Q....
Do you see any advantage in having an air or fluid pipe going to the bottom of the battery for electrolyte circulation as I have seen some commercial batteries or do you believe that proper charging and equalising takes care of that?
No, each of the 13off SOLID rigged plates are in a thick geoyextile felt, non woven, sock. I have allowed 5mm internal clearance for the plate sides, and the plate faces are not tight against each other.
Its a proportional relationship between amount of lead plates to Acid required and circulation.
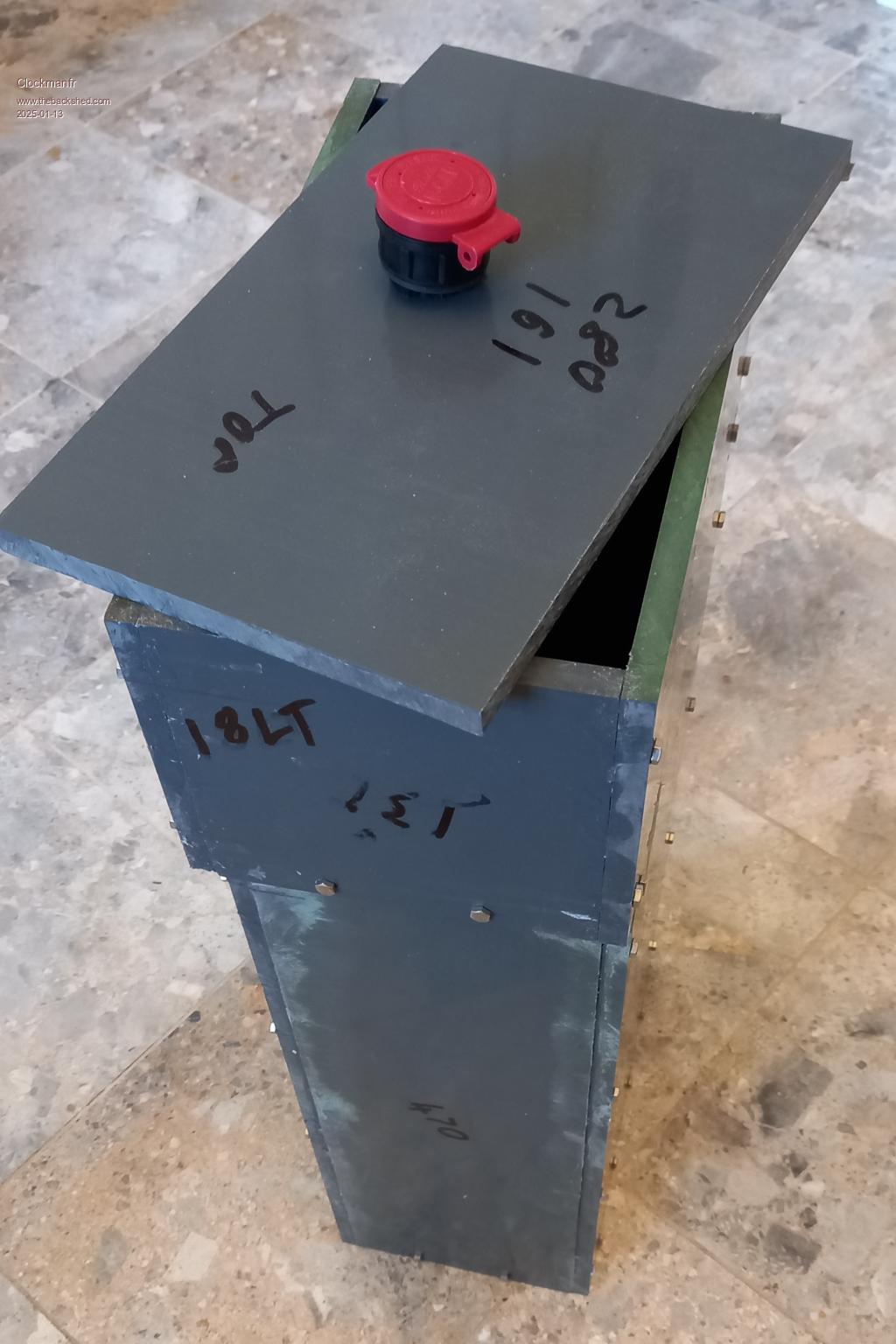