Back
The first test.
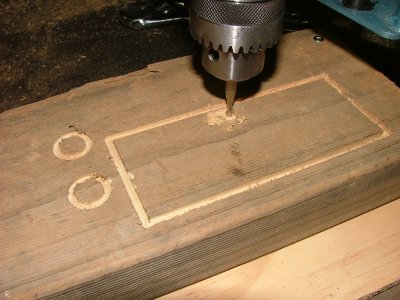
I was having problems with the stepper
speed, or lack of. I found some better stepper drivers
and motors at http://www.oceancontrols.com.au/.
The new drivers have built in current regulation and
a half step option. Once fitted the router started to
perform much better.
But I was still having problems. The
rout was very rough, any change in timber density (
grain ) made the router tip wobble. I worked out there
was too much movement or slop in the gantry, but this
was not easy to fix. I was considering abandoning the
current design and starting again with some industrial
linear bearings and good worm drives. But the cost was
scary.
In my research to find a supplier for
the parts I needed, I stumbled across http://www.cnczone.com.
This site has a forum where members talk about their
own router designs and problems. I noticed most of the
routers were running spindle speeds of over 15,000 rpm.
Hang on, my spindle only had a maximum speed of 3,000
rpm!
So I went out and bought a cheap plunge
router. The router has variable speed, 600 watt motor,
2 year warranty and cost a staggering $50. What the
hell, it if didnt fix the problem I could use it elseware
in the workshop. While I was at it, I bought a small
engraving tool.
I made an adapter for the Z axis to
take both machines, with the engraver mounted below
the router. So when I want to rout I take the engraver
off, and visa versa.
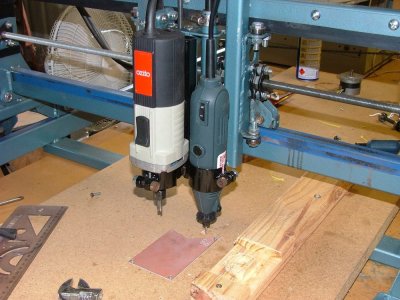
Well this made all the
difference. The cnc router now has no problems with
wobble, and give a nice clean cut. The machine was now
usable. So I made a sign for the dog from a bit of old
hardwood.
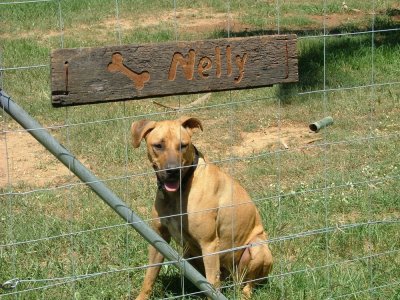
Next in the list of things
to do was improve the stepper speed more. My maximum
travel speed was only 200mm per minute, a bit on the
slow side. To home the machine could take several minutes.
Some research hinted that I need a much higher bus voltage,
and Terry confirmed this for me.
So
I modified a couple of computer AT power supplies. First
I isolated the -ve output from ground in one of the
supplies. This was then connected to the 12v output
on the other power supply, and gave a total voltage
of about 24 volts. The output of each powersupply was
also "tricked" up to 14volts, giving 28volts
total. I crammed the two power supplies into the electronics
box and fired it up. What a difference it made, my travel
speed was adjusted up to 350mm per minute, now we were
moving!
Next I upgraded the PC
driving the CNC router. I was using a PII 300MHz machine
with 256M ram. I had a AMD 2.4GHz cpu and mainboard
doing nothing, so I built a new PC and installed the
software. This increased the CNC speed to 400mm per
minute, not a big step, but the software ran a lot smoother.
Next
|